P3034
Modern Broiler House Heating Systems
Why Are Heaters Used in Broiler Production?
The first stage of broiler production is called brooding and lasts approximately 8–14 days, depending on the integrator and weather conditions. During brooding, chicks are usually housed in only a portion of the building, and heaters are used to create suitable temperatures for growing birds. A comfortable thermal environment for young chicks during brooding is critical to the overall performance of a broiler chicken.
For the first 4–7 days of life, broiler chicks are poikilothermic, which means they cannot maintain a stable core body temperature (Brody, 1945). Heaters are especially important during this time to ensure that building temperatures do not fall too low. For optimum performance, chicks should remain in the thermoneutral zone, or a range of temperatures at which they do not have to actively regulate body temperature. If house temperatures fall too low, performance will suffer because chicks will often huddle and fail to actively seek out feed and water, and/or they will metabolize energy in the feed to remain warm and not for growth. A bird’s body temperature can drop to around 73°F before death occurs (Pescatore & Jacobs, 2014). If house temperatures are too high, decreases in performance will occur as chicks expend energy trying to stay cool through panting or by holding their wings away from their bodies. Elevated air temperatures can also reduce feed consumption. The upper lethal limit on body temperature is 113–117°F (Pescatore & Jacobs, 2014).
The next stage of production is called growout, at which time birds are allowed full use of the building. Heaters are often used during growout, but not as frequently as during brooding. Growout usually lasts until the birds are 35–63 days old and is determined by the integrator and the size of the bird being grown.
The primary objective in managing a poultry house environment is to create a space that is comfortable for the birds and optimizes growth. This can be challenging and resource-intensive, especially during brooding in cold weather when high temperatures are required in large, open, and perhaps drafty brooding chambers. To further complicate the issue, target house temperatures gradually decrease for approximately the first 4 weeks. As birds get older, their thermoregulatory systems mature and they no longer need the high house temperature that younger birds require. The body heat generated by older, larger birds also helps to heat the air. House temperature regimes are prescriptive, breed-dependent, and generally determined by the integrator. Broiler management guidelines recommend starting air temperatures of 86–93.2°F at day 1 (Aviagen, 2014; Cobb-Vantress, 2012). Every day thereafter, the guidelines recommend decreasing air temperature incrementally until a final temperature of 65–70°F is reached at around day 27 and maintained for the remainder of the growout. Some integrators growing large broilers (60+ days of age) may lower the final temperature a few additional degrees to account for the large amount of heat being produced by the birds.
Broiler House Heating Systems
Two types of supplemental heating methods are commonly used in poultry facilities: radiant heaters and forced-air space heaters. Space heaters heat the air in the building, while radiant heaters heat the birds and litter directly. Both types of heating systems have been shown to be successful at raising chicks; however, in recent years, many integrators have moved away from forced-air heaters because they do not do an adequate job of directing heat toward the floor and warming the litter. Warm litter or bedding material on the floor is critical to helping the baby chick maintain its body temperature the first few days after hatch. Radiant heaters do a much better job warming the floor than do forced-air heaters. Alternative heating systems such as biofuels (e.g., wood, corn) will not be discussed in this publication.
What Is Radiant Energy?
Radiant energy travels through the air on electromagnetic waves and must come into contact with an object to produce a heating effect. When it strikes an object, the radiant energy is absorbed and converted into heat. Examples of radiant energy include sunlight, infrared radiation emitted by people and animals, and heat emitted by a campfire. The amount of radiant energy emitted is temperature-dependent, with more energy being released at higher temperatures. Infrared cameras detect radiant heat emitted from surfaces and can be used to show the surface temperature of objects.
Radiant heaters used in poultry houses create a comfortable environment for chicks in two ways. First, when the heaters are on, the chicks directly absorb the energy emitted. Second, the litter absorbs energy from the heaters, which causes its temperature to rise. The heated litter creates a microclimate near the litter that is suitable to chicks. Litter temperatures directly below a radiant heater can reach 130°F and decrease with distance from the heater (Pescatore & Jacobs, 2014). When radiant heaters are used, air temperatures at chick height are not uniform throughout the house, and locations away from the immediate vicinity of the heater may be 5–10°C cooler. The temperature gradient created by radiant heaters provides a range of thermal comfort options for chicks.
Heater Gas Supply Pressure
Radiant heaters operate on natural gas or propane and have varying input ratings depending on the style of the heater and the manufacturer. They can be broken into two broad categories based on the required gas supply pressures. Low-pressure heaters typically operate at gas supply pressures of 5–14 inches of water column (in. WC) for natural gas and 11–14 in. WC for propane. High-pressure heaters operate at about 138.5 in. WC (5 psi) for both propane and natural gas. Heaters that operate at low pressures are more common because many poultry houses are not equipped to handle the elevated pressures needed for high-pressure heaters. Each manufacturer will specify minimum and maximum operating pressures for its own equipment. It is critically important that all gas tanks, plumbing, and pressure regulators be sized to provide the proper gas pressure to every heater in the broiler house.
Radiant Brooders
Radiant brooders used in poultry houses are open-flame heating systems, which means that the flame is visible and that the source of air for combustion comes from within the building. These two types of open-flame radiant brooders will be discussed in this section: circular radiant brooders and rectangular radiant brooders. Circular radiant brooders (Figure 1) are very common and are manufactured by several companies, while the rectangular radiant brooder is a patented design of a single company.
Circular radiant brooders are most often installed over feed and water lines to create a comfortable thermal environment that encourages chicks to eat and drink. In a typical 40- by 250-foot brood chamber, at least 14 radiant brooders are usually installed. Additional brooders will also be installed in the off end in case supplemental heat is needed after the brooding phase is over and birds are turned out (Figure 2). The number and size (Btu input) of brooders required will vary. This is determined by individual integrators and will be listed in the integrator’s housing specifications. Circular radiant brooders are usually spaced 25–40 feet apart in the brood chamber and 5–7.5 feet above the litter. They must be raised to allow clearance for people and machinery to operate during catch and cleanout, and then lowered before the next flock.
The canopy, emitter, and burner are the most critical parts of a circular radiant brooder. Circular aluminum or stainless steel canopies reflect heat to the chicks and range in diameter from 31–37 inches. Canopy temperatures range from approximately 200–400°F (Linhoss, unpublished data). All circular radiant brooders also contain a stainless steel emitter that is heated by combusted gas and designed to “emit” radiant heat to the litter. Emitter temperatures can range from 900–1,100°F (Linhoss, unpublished data). Sizes and shapes of emitters vary between manufacturers, but they all create a circular heating pattern with the highest litter temperatures produced closest to the brooder. Cast-iron burners are commonly used to control and shape the flame so that it heats the emitter evenly.
Most circular radiant brooders come in either pilot or direct-spark ignition. Direct-spark ignition uses a high voltage electrical arc or spark between two electrodes to light gas flowing to the burner. Since fuel is not used to keep a pilot light continually lit, spark-ignition brooders can save an estimated 1,500–2,000 Btu per hour at times when the house does not need supplemental heat. All igniters are equipped with a gas safety shut-off value to stop the flow of gas if the burner fails to light.
Circular radiant brooders are controlled by a thermistor, an inexpensive sensor that is used to measure air temperatures. In general, one thermistor is used to control a “zone” that consists of three to four brooders. Air temperatures can vary throughout the brood chamber, and zone control ensures that heat is provided only where it is needed. Recommendations for locating the temperature sensors vary by manufacturer, but most recommend placing them 8–15 feet from the center of the nearest brooder and 6–12 inches above the litter. Since brooders warm the floor with radiant heat but the sensors measure air temperature, growers must carefully observe birds to determine proper control settings.
An 80,000 Btu per hour open-flame radiant brooder is also available. It is rectangular in shape and the canopy, emitter, and burner are designed differently than those on circular radiant brooders (Figure 3). It has two adjacent rectangular emitters that create a rectangular-shaped heating pattern on the litter, as opposed to the circular pattern created by radiant brooders. Since these brooders are rated at twice the heat capacity of radiant brooders, they heat a larger area of the litter and fewer units are required in a typical brood chamber. The manufacturer recommends six brooders installed in 40–50-by-200-foot brood chambers; seven in 40–50-by-250-foot brood chambers; and 14 in 50–66-by-300-foot brood chambers. The recommended distance between brooders depends on the size of the house and varies from 34 to 49 feet. Rectangular brooders are available in high-pressure and low-pressure models. The recommended elevation above the litter is 7–9 feet. Since this heater has twice the heat capacity of a round radiant heater, it must be placed higher in the house to reduce the likelihood of extremely hot floor temperatures directly below the heater. Care must also be taken to observe prescribed clearances above and on the sides of the heaters.
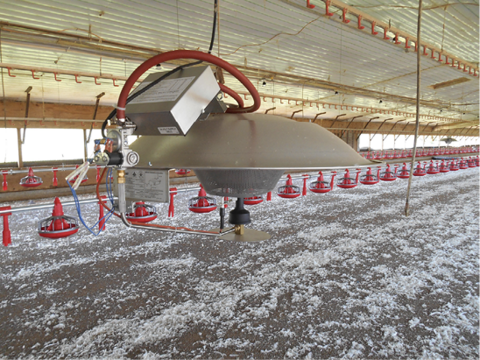
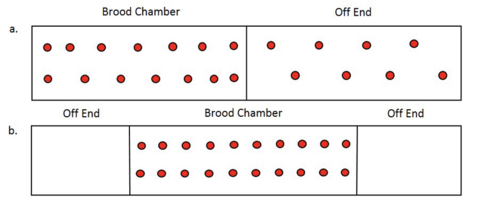
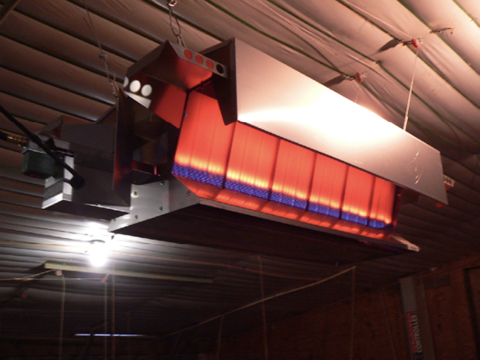
Radiant Tube Heaters
Tube heaters are closed-flame heating systems (Figure 4). They source combustion air from outside the house, and the flame is enclosed in a metal box connected to a long, metal tube. A fan forces hot combustion gases through the tube, which radiates energy to the litter. Exhaust gases are typically discharged into the house and then removed through the ventilation system. Tube heaters range in heat capacity from 50,000 to 150,000 Btu per hour. Radiant tube heaters are available in lengths from 20 to 60 feet, but most used in the poultry industry range from 40 to 50 feet. They are mounted lengthwise down the center of a house, usually about 10–12 inches below the apex of the ceiling. Unlike round radiant brooders, radiant tube heaters do not have to be raised or lowered during any stage of the production process. They also heat a larger portion of the litter than round radiant brooders and require less overall maintenance because there are fewer units installed in a typical brood chamber (Figure 5).
Tube temperature near the firebox can reach 1,000°F and may be 350–400°F 40 feet away (Donald & Czarick, 2010). The tubes radiate heat downward to the birds and litter, while reflectors protect the ceiling and reflect any upward-directed radiant energy back down to the chicks. The mounting height and reflector geometry determines the width of heat distribution across the floor. Tube heaters should be capable of distributing heat to the outer water and feed lines. Litter heat distributions tend to be oval-shaped because of the higher temperatures near the firebox. As with radiant brooders, tube heaters produce temperature gradients that allow chicks to select the area that provides the most comfort.
Some tube heater models are dual-stage and can operate a low- and high-level output. A dual-stage tube heater may operate at 75,000 Btu per hour at the low output and 125,000 Btu per hour at the high output. For most of the year, the heater will operate at the low output, but the high output is available if needed during extremely cold periods. Operating at the lower output saves fuel because there will be fewer on/off cycles and longer run times. When a tube heater first starts up, the tube has to heat up to its operating temperature to provide maximum radiant heat. The process of heating up the radiant tube uses energy in the fuel that could be directed to the birds. Reducing the number of on/off cycles reduces the fuel used solely to heat up the radiant tube to its maximum operating temperature.
Radiant tube heaters operate at low-supply gas pressures. Direct spark is the most common type of ignition system. Distance between heaters in the brood chamber is dependent on the size of the house and the heaters but is commonly around 20 feet. The distance of heaters from the litter is dependent on the height of the apex of the ceiling but is generally around 10–12 feet. As with radiant brooders, thermistors are also used to control radiant tube heaters. A common recommendation is to line the thermistor up with the midpoint of the heater and hang it about 12 inches off the ground between the outside water and feed lines (Donald & Czarick, 2010).
A disadvantage to both rectangular and radiant tube heaters is that if one fails, approximately 25 percent of the total heat input into the house is lost, which could lead to chilled chicks, wet litter, and a host of other problems that could significantly affect production. With round radiant brooders, there is less chance of a major disruption in production if one unit fails.
Several manufacturers are currently marketing “radiant tube brooders.” Like radiant tube heaters, they contain a firebox, a radiant tube, and a reflector (Figure 6). The major difference is in how the radiant tubes and reflectors are configured. Radiant tube brooders are essentially radiant tube heaters that have been folded in half, so they are only 9–20 feet long. There is a tube that is doubled back on itself on each side of the heater. The tubes are mounted in a V-shaped pattern, and each one has its own reflector. The concept behind the V-shape design is to create a wide, rectangular heat pattern with better uniformity of heat distribution along the length of the house and better floor coverage from side to side across the house.
Radiant tube brooders range in heat capacity from 40,000–90,000 Btu per hour. They require the same gas supply as radiant tube heaters and operate on propane or natural gas. Single- and dual-stage models are available. As with radiant tube heaters, direct spark is the most common type of ignition system. The installation guidelines recommend six heaters installed in 40–50-by-200-foot brood chambers, seven in 40–50-by-250-foot brood chambers, and 14 in 50–66-by-300-foot brood chambers. A distance of 40–60 feet is recommended between radiant tube brooders. It is recommended that thermistors be located approximately 10 feet from the side of the heater and ideally between the feed and drinker lines.
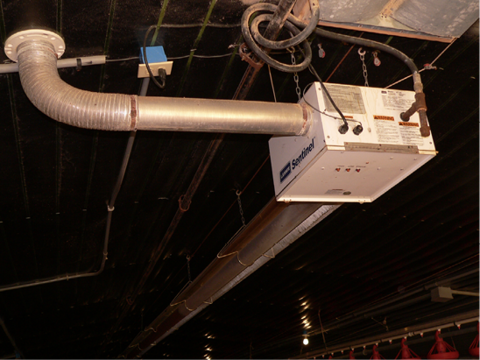
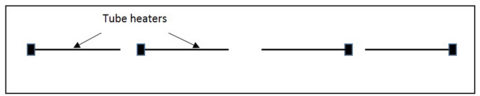
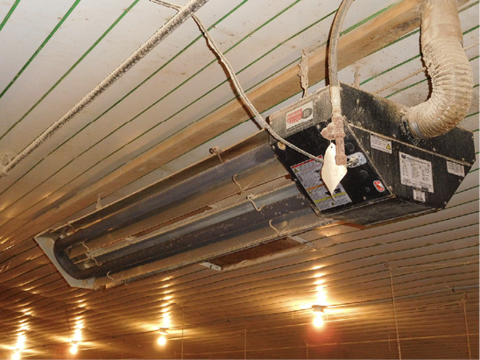
Forced Hot-air Heaters
Forced hot-air space heaters used in poultry facilities are rated between 30,000 and 325,000 Btu per hour. Space heaters use energy released from the combustion process to heat air. Fans within the unit then distribute the hot air throughout the house. Space heaters are typically installed on one sidewall of a broiler house, which allows for better heat distribution throughout the house. They perform well during the later stages of growout when birds can tolerate colder temperatures, but they may not maintain the warmer temperatures near the litter needed during early brooding due to thermal stratification of air (Pescatore & Jacobs, 2014). Thermal stratification occurs when the hot air blown into the house by the space heater rises to the ceiling and creates a vertical temperature difference in the house. Stir fans are commonly installed near the ceiling to circulate this hot air back to the litter where it is useful to chicks. In some instances where adequate temperatures cannot be maintained, both space and radiant heat systems are used.
Space heaters operate at low gas supply pressures. It is common for three to four 225,000–250,000 Btu per hour heaters to be installed in a brood chamber. Most models are variable-rate input and can operate down to about 60 percent of their rated capacity. For example, the input for one space heater model is variable from 160,000–250,000 Btu per hour. Space heaters are primarily equipped with direct-spark or hot-surface ignition systems. Select models are available with pilot ignition. Hot-surface ignitors initiate combustion of incoming gas by using an element that heats up to approximately 1,800°F when energized by an electrical signal. While many older houses still make use of forced-air heaters, most new house construction and renovation projects on older houses require radiant brooders or tube heaters as the heat source.
Conclusions
The primary concerns among growers with regards to heating systems are 1) Do the heaters produce a thermal environment that maximizes bird performance and comfort? and 2) How much will it cost to produce a suitable environment? To put it into perspective, a single broiler house can use 3,000 to 5,000 gallons of propane in a year. That’s around $32,000 a year in propane costs for a four-house farm. Over 50 percent of the fuel consumed is during the first week alone when the highest temperatures are required (Flood Jr. et al., 1994).
Both radiant heaters and forced-air space heaters have been successfully used to create thermal environments suitable for chicks during brooding. In recent years, radiant heaters have become the preferred method of providing heat during brooding because they provide a range of thermal comfort options for chicks and have been shown to be cost-effective to operate. Despite their prevalence in poultry houses, no estimates of efficiency for radiant heaters in brooding applications are available. Quantitative research into radiant heater efficiencies and floor-heat distribution patterns could benefit the industry by helping growers make better decisions about selecting heating equipment and managing the thermal environment.
Brooder type |
Round radiant brooder |
Rectangular radiant brooder |
Radiant tube heater |
Radiant tube brooder |
Forced-air space heater |
---|---|---|---|---|---|
Rated Capacity (Btu/hr) |
|||||
Pilot ignition |
40,000–42,000 |
80,000 |
– |
– |
– |
Direct spark |
40,000–42,000 |
80,000 |
50,000–150,000 |
39,000–90,000 |
30,000–325,000 |
Hot surface ignition |
– |
– |
– |
– |
30,000–325,000 |
Fuel consumption |
|||||
LP (gph) |
0.43–0.46 |
0.87 |
0.54–1.63 |
0.42–0.97 |
0.66–3.25 |
Natural gas (cfh) |
37.8–40.0 |
75.5 |
47.2–141.5 |
39–90 |
30–325 |
Butane/propane mix (gph) |
– |
0.87 |
– |
– |
– |
Gas pressure requirements (in WC) |
|||||
LP–low pressure |
11–14 |
11 |
11–14 |
11–14 |
11–14 |
LP–high pressure |
138.5 (5 psi) |
138.5 (5 psi) |
– |
– |
– |
Natural gas–low pressure |
5–14 |
5.5 |
5–14 |
5–14 |
7–13.5 |
Natural gas–high pressure |
138.5 (5 psi) |
138.5 (5 psi) |
– |
– |
– |
Burner pressure (in WC) |
|||||
LP–low pressure |
10–11 |
– |
10 |
10 |
– |
LP–high pressure |
138.5 (5 psi) |
– |
– |
– |
– |
Natural gas–low pressure |
4–7 |
– |
3.5 |
3.5 |
– |
Natural gas–high pressure |
138.5 (5 psi) |
– |
– |
– |
– |
Electrical requirements |
24 VAC/60HZ /1– 120 VAC/60HZ/1 |
24 VAC/60HZ /1–120 VAC/60HZ/1 |
120 VAC/60HZ/1 |
120 VAC/60HZ/1 |
120 VAC/60Hz/1 |
Minimum clearance to combustibles (in) |
|||||
Sides |
36 |
48 |
52–84 |
36 |
12–20 |
Above |
18–36 |
12 |
10–12 |
10–12 |
12–20 |
Below |
48–54 |
72 |
47–108 |
40–69 |
12–20 |
Dimensions (in) |
|||||
Height |
14–18 |
13.25 |
9 |
13–15 |
18–3 |
Width |
– |
22 |
18–31 |
24–25.5 |
14–24.5 |
Length |
– |
48 (4 ft) |
240–720 (20–60 ft) |
180–240 (9–20 ft) |
252–432 (21–36 ft) |
Canopy diameter |
34–37 |
– |
– |
– |
– |
Net weight (lb) |
18–28 |
55 lb |
81–265 |
103 |
52–150 |
Operational guidelines (ft) |
|||||
Elevation from litter |
5–6 |
7–9 |
6–14 |
6–9 |
– |
Space between heaters |
25–40 |
40–60 |
20 |
40–60 |
– |
Ventilation (cfm) |
200–468 |
– |
140–500 |
155–360 |
– |
References
Aviagen. (2014). Arbor Acres Broiler Management Guide (opens PDF file). Aviagen Group. Huntsville, AL.
Brody, S. (1945). Bioenergetics and Growth. New York, U.S.A.: Reinhold Publishing Corporation.
Cobb-Vantress. (2012). Broiler Management Guide (opens PDF file). Cobb-Vantress, Inc. Siloam Springs, AR.
Donald, J., & Czarick, M. (2010). Report from the field: Radiant Tube Heaters for Poultry Houses.
Flood Jr., C.A., Koon, J.L., Trumbull, R.D., & Brewer, R.N. (1994). Weekly heat usage for broiler chickens. Applied Engineering in Agriculture, 10(2), 285–286.
Pescatore, A.J., & Jacobs, J. (2014). Poultry Production Manual. College of Agriculture, Food and Environment. University of Kentucky Extension. Lexington, KY.
Publication 3034 (POD-10-23)
Reviewed by Jessica Drewry, PhD, Assistant Professor, Agricultural and Biological Engineering. Written by John Linhoss, PhD, former Extension Associate III, Agricultural and Biological Engineering; Joseph Purswell, PhD, Research Agricultural Engineer, USDA ARS Poultry Research Unit; and Daniel Chesser, PhD, Assistant Professor, Agricultural and Biological Engineering.